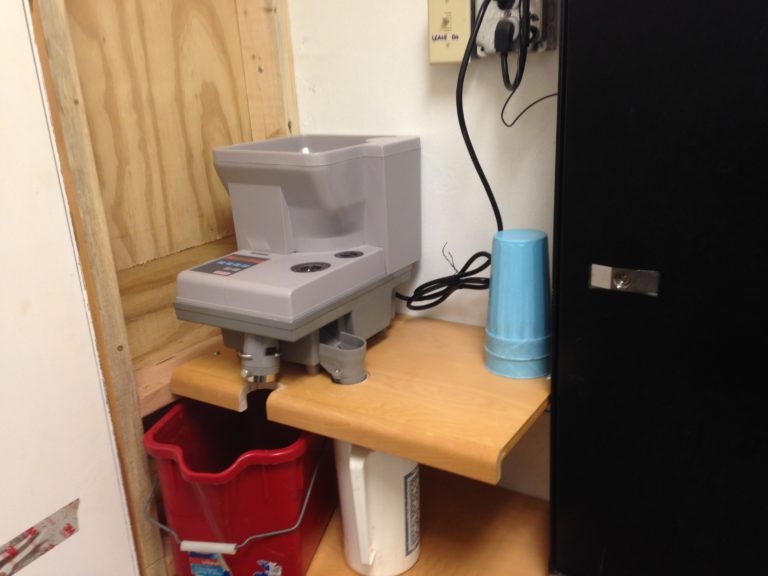
American Changer CC-302 Coin Counter Install
I talked to American Changer and they explained how their counters are built for years of use. American Changer is the Parent Company of Hoffman Mint, the token manufacturer and they use the same coin counter in their factory to count the orders before shipment.