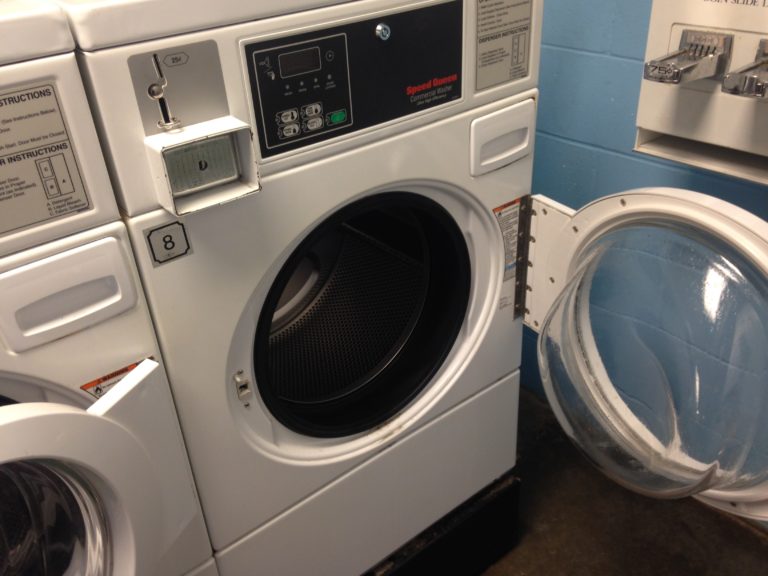
Speed Queen Washer Shock Absorber Change
Speed Queen Washer Shock Absorber Change Over time the shock absorbers in the Speed Queen / IPSO soft mount washers will wear out. At this point, they become just a set of springs. …
Speed Queen Washer Shock Absorber Change Over time the shock absorbers in the Speed Queen / IPSO soft mount washers will wear out. At this point, they become just a set of springs. …
We have been noticing water on the floor behind a couple of Dexter washers lately. This morning I headed in to see what the problem was. Last week we had…
Washing machine water leak. Speed Queen Top Loaders There was a small amount of water under one of the Top Load washers. I had been working on a machine beside it and after I was…