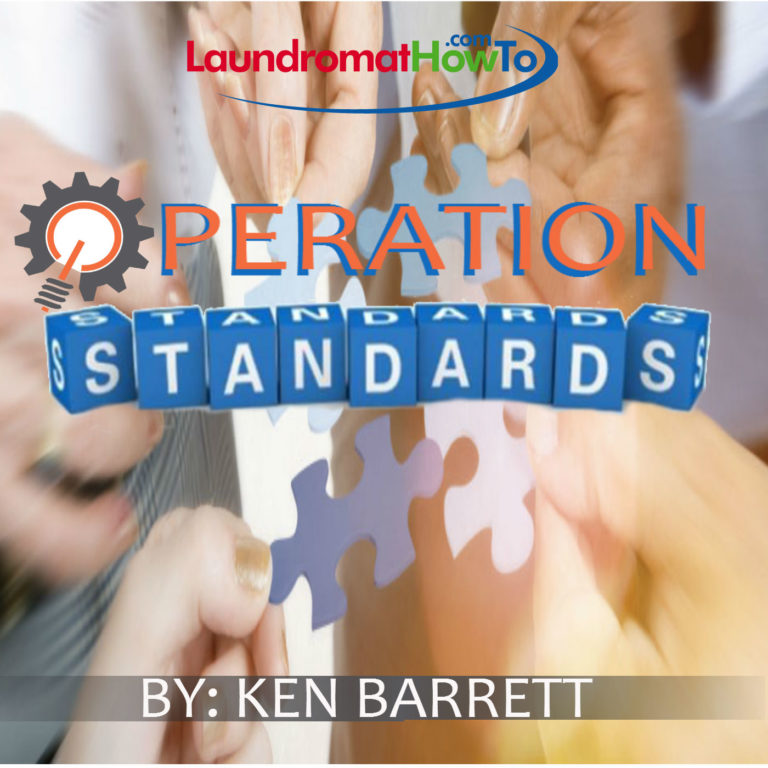
Episode 42 – Operation Standards
In the Drop Off Laundry business that many coin Laundry Owners have or are considering starting this is an obstacle that needs to be addressed early on.
POS- With Brian Henderson Part 2 This is the second part of my interview with Brian Henderson and…
IPSO / Speed Queen Washer Not Draining A complaint we receive occasionally is that the small Horizon style front load washers “Didn’t spin my clothes out”. There may be a couple of issues that cause…
I recently returned from the Clean Show in Atlanta and stopped by one of my stores to see how things went while I was gone. I checked a few things…